Giave Gialux UV/LED/EB Flexo. Bridge the Gap between Digital Print and Flexo Printing.
New Generation Flexo Press with GREEN SUSTAINABLE TECHNOLOGY. UV/LED Low Migration Inks are here.
Flexo Printing without solvents or water base inks and with higher print quality while reducing energy costs and emissions.
In 2024, Giave (Barcelona, Spain) rolled out a new, better way to flexo print for on-demand flexible packaging with Gravure and Offset quality without solvents.
A new “all-Servo” UV/LED Mid-Web flexo press for indirect food contact, cosmetics, pharmaceuticals, shrink sleeve, and in-mold labels, that can also be configured for folding cartons and paperboard for offset print quality, roll to roll.
Value-added capabilities such as Cold Foils, spot register matte varnish and much more can be applied in line.
This all-Servo drive system matches CI register accuracy with new tension controls and web handling. This press fits the need for a more versatility press over a wider range of packaging requirements when compared to Digital Printing.
Comparable results to conventional inline flexo label presses common for labels vs flexible packaging.
The long web path on a label press increases material waste during setup. Additionally, down gauging of materials increases problems with tension control. By adding sophisticated setup features and tension controls to a label press, traditional presses have driven up the cost of inline presses. Most importantly, a mid-web press in the range of 34”, 42”& 50” with a larger maximum repeat will provide the capability for a wider range of stand-up pouches and flexible packaging than a 27” wide press. All the above has led to the development of an entirely different approach to flexo printing for short runs.
This NEW all-servo drive system combined with Siemens' state-of-the-art controls is the basis for this new integrated process control. The coordination of more than 60 axes, depending on the machine configuration, is done by a high-end motion controller from Siemens with an integrated register control.
A BETTER WAY TO FLEXO PRINT for ORDER ON DEMAND with GRAVURE QUALITY
How will buying habits change as a result post-COVID-19 and the developing Circular Packaging Economy? Increased shorter runs without sacrifice in print quality. There is a lot of misinformation about how short-run flexible packaging and multiple SKUs can be profitably printed. Central Impression (CI) presses became popular because of register accuracy; however, the CI press is not operator friendly for shorter runs even with sophisticated setup features. Mid-web CI presses were offered as a short run solution, but this approach has not gained widespread acceptance because of the need for more versatility over a wider range of packaging requirements. The inline label press is more operator friendly; however, the long web path increases material waste during setup. Additionally, down gauging of materials increases problems with tension control. By adding sophisticated setup features and tension controls, this has driven up the cost of inline presses. Most importantly, a mid-web press in the range of 34”-40” with a larger maximum repeat will provide the capability for a wider range of stand up pouches and flexible packaging than a 27” wide press. All the above has led to the development of an entirely different approach to a flexo printing for short runs.
Versatile UV/LED Mid-Web Flexo with Digital Print Enhancements
Lower energy costs, Lower carbon footprint, Reduced operating costs
Extended Gamut color mastery & ink cost savings.
Compact footprint with short-web path that reduces material waste.
Lower profile: operator-friendly with all-servo drive system that matches CI register accuracy
Removing the CI drum, we eliminate the problems of Drum heat build-up and cleaning down-time. Removal also prevents common CI drum UV light from bouncing back.
Printing both front and back of the web without turn bars and Anti-Bounce technology.
Unique ability to safely make ready decks while the press is running.
Apply Barrier Coatings and Overprint Varnishes in-line.
Reduced fire and explosion hazard
Automatic deck positioning and register
Solution to SHORT RUN FLEXIBLE PACKAGING
"SKU PROLIFERATION" and SHRINK SLEEVES
UV/LED/EB FLEXO-THE NEXT DISRUPTIVE TECHNOLOGY
How flexible packaging materials are printed is an area that needs close scrutiny for the reduction of VOC solvent emissions, lower energy costs and the “Circular Economy” in packaging. The versatility of today’s servo driven flexo press with sophisticated tension controls opens the way to a new approach to short run package printing once possible only with a CI press. Improved UV/LED inks are coming on stream every day to meet the demand to eliminate solvent inks and at the same time produce extremely high quality flexo printing. The ability to use extended gamut colors becomes easier because of the stability of the ink on press throughout the run and consistency from one run to another. Reduction of spot colors and color matching can also lead to a reduction in setup waste. A reduced environmental footprint using food packaging compliant UV/LED inks is possible if converters can overcome the fears associated with radiation curing inks.
“UV LED formulated inks, coatings and adhesives as well as UV LED curing systems and the presses specifically designed to utilize the technology have advanced tremendously in the last ten years. Formulators are stepping up to expand UV LED offerings in order to meet growing and diverse print production demands. ”
Versatile/Efficient: UV/LED Extended Gamut is easier, consistent
Food safe: Complete EB curing for indirect food contact
Reduce costs: UV/LED/EB ink with reduced photoinitiator
No contamination: Zero backside ink in printed rolls
Sustainable Zero solvents: No emissions impact; retained solvents
Sustainable Less energy: no dryers necessary
Waste Reduction Features: Shorter web path make ready
Backside print: front and back without turn bars
Uptime: Unique safe make ready deck access during a run
Value Added:Cold Foils, register matte varnish and much more
TWO MARKET OPPORTUNITES:
UV/LED food packaging compliant inks
DUAL CURE Hybrid Press
UV/LED/EB inks with reduced photoinitiators that can be completely deep cured with a final Electron Beam unit. Between colors UV/LED lamps can partially tack the ink, eliminating the wet on wet ink process. Final cure is with the E-Beam unit eliminating any fears of backside ink offset in printed rolls, migration or food contamination.
1) UV LED system
An increasing number of UV LED system suppliers have recently engineered an incredibly broad range of UV LED designs in order to meet the diverse needs of curing applications across both printing and non-printing applications. In many ways, the industry is now spoiled for choice. Systems intended for one market segment and set of applications, however, are not necessarily suited for another. Properly selecting a UV LED curing system that meets the needs of the print product range for a given press as well as the intended process conditions is incredibly important, yet too many UV LED system suppliers do not provide enough information regarding how UV LED output potentially impacts cure. This can make it difficult for OEMs and end users to navigate the sourcing process and make informed purchasing and development decisions. This unnecessarily stalls printing innovation and UV LED adoption. In cases where the technology is more than viable, an improperly sourced and integrated system can make it appear as if the technology isn’t ready, even though it is.
Formulation requirements, working distance and run speed are the primary drivers of the UV lamp head’s spectral output (wavelength), irradiance (intensity) and energy density (dose) that must be delivered to the print surface for suitable polymerization or cure. Consequently, wavelength, peak irradiance at a known location and energy density at a defined line speed should be specified by UV LED system manufacturers and confirmed by the OEM press manufacturer for each UV LED product being considered for the press. OEMs who work closely with formulators and UV LED system suppliers during development in order to ensure that the correct UV LED system has been matched to the needs of the application and formulation are the ones who are exceeding customer expectations when it comes to UV LED curing performance. When the correct UV LED system is utilized, cure is consistent, repeatable and reliable. (end of quote) So Why Measure? Because there are no direct, on-line methods of determining degree of cure. In addition, since there is substantial variation in types of UV lamps, age of the lamps and ink used, the UV exposure conditions must be monitored and correlated with the cure result for the purpose of verifying that the exposure is maintained within predetermined limits. Any fears of inks not being fully cured, however, are being overcome by new technology that delivers consistent output as a way of better ensuring full cure with migration issues under control.
For the above reasons, an inline flexo press equipped with UV/LED lamps for labels is not necessarily the right system for all types of flexible packaging at required profitable speeds that are sufficiently cured.
UV Curing on a GIave Press
“Lamp head designs have gotten longer and wider and have been engineered to efficiently emit more UV output. Presses equipped with UV LED lamp heads are running faster and are better leveraging the technology to solve long standing integration and process challenges. This includes tighter lamp head form factors that more easily integrate into presses; significantly reducing heat transfer compared to conventional bulb based systems which can warp films and damage press components; providing consistent UV output that spans production runs of days, weeks and years; and longer UV LED wavelengths that better penetrate through film constructions and deep into formulations to better cure densely pigmented formulations and especially white inks. ”
2) Second option": Dual Cure-Hybrid
UV/LED/EB inks with reduced special photo initiators can be completely deep cured with a final Electron Beam unit. Between colors UV/LED lamps can partially cure or tack the ink, eliminating the wet on wet ink process. Final cure is with the E-Beam unit eliminating any fears of set off backside ink in printed rolls, through migration and food contamination. The cost of E-Beam units can be justified by the reduction in photo initiators and operating costs.
REDUCED OPERATING COSTS
The ability to execute fast changeovers and process a wider range of substrates including combinations of paper, film, foil and thinner gauge flexible substrates that are extensible in nature in this ever changing environment, demand a more flexible approach to how these materials are processed. Narrow web companies benefit from the fact that most manufacturers, especially those operating in the food and drink sectors, have widely embraced controlled inventory costs. With the ability to produce both flexible packaging and shrink sleeves on the same press, this increases the ability to yield a faster payback if volumes require this flexibility. For wide web printing, this translates into more frequent runs, so converters need to adjust to increase profitability. Converters should consider the best approach to be more profitable in both short and long runs, rather than just stay with the way it has been done in the past.
Extended Gamut with UCR (Under Color Removal) can reduce ink costs up to 28%
A standard 7 color ink set, CMYK, orange, green and violet cuts pre-production lead times by removing the need to qualify new inks every time you go to press. You’re eliminating things like wash-up time on press, and scrap with quicker set-ups, not to mention the savings in ink waste with multiple wash-ups daily. By using UCR color separations you can save between 10%-28% in ink costs. Additionally, run speeds can be higher because of the reduction in ink layers leads to faster curing.
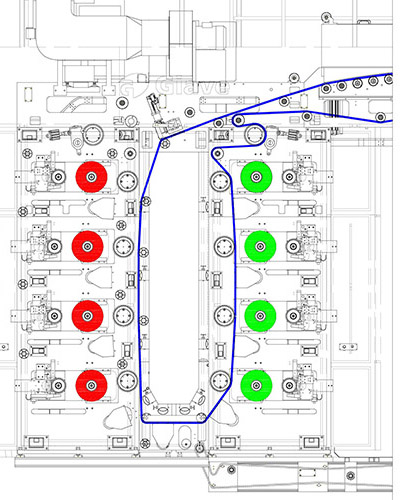
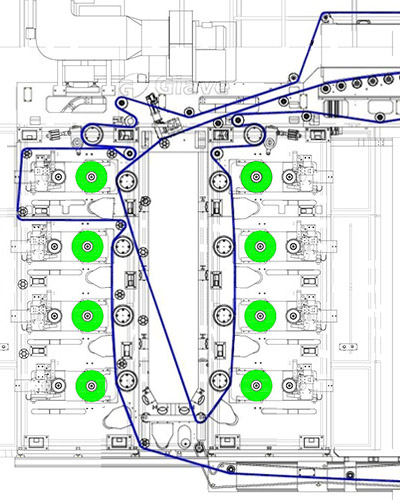
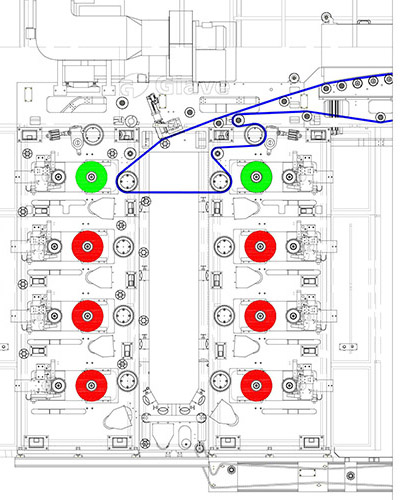
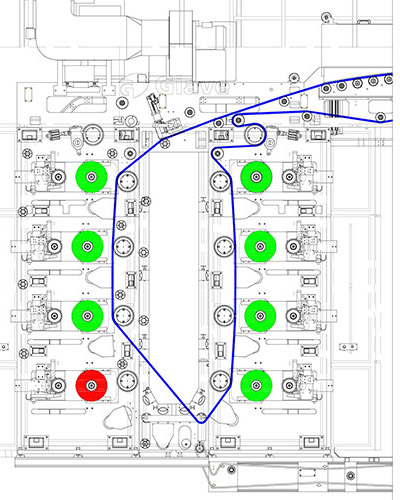
Low to zero volatile organic content (VOC) and hazardous air pollutants (HAP)
UV cured resin generates up to 87% less carbon Dioxide, compared to thermal curing Water or Solvent systems.
No dryers: less energyEstimated 80% total energy reduction in Btu including natural gas and electrical power
Lower profile: operator friendly
Less material waste: shorter web path
Reduced fire and explosion hazard
No CI drum requiring constant cleaningCI drum can cause unsafe UV light bounce back
Backside print: front and back without turn bars
All Servo
A NEW all-servo drive system that matches CI register accuracy. The combination of state-of-the-art control and drive electronics from Siemens is the basis for this new integrated process control. The coordination of far more than 60 axes, depending on the machine configuration, is done by a high-end motion controller from Siemens with an integrated register control in combination with a fail-safe Simatic (Siemens).
Profinet and Siemens Advanced Systems
On a CI the CI drum is the master drive and all other drives follow it. On the Giave (Siemens) system, all drives are master drives and they talk to each other with real time communication via Profinet IRT (Isochronous Realtime). Consistently high print quality with the Siemens integrated register control with minimal start-up waste is possible in some cases to only about 30 feet of set up waste.
Learning Error Compensation
Another possibility of improving the quality via the drive system is the function Learning Error Compensation. (LECo). The self-learning control algorithm uses the drive control behavior to detect cyclic disturbances caused by the typical vibrations of flexographic printing due to the the printing plate gaps (bouncing). LECo compensates for this automatically and thus their negative impact on the print. Last, but not least: In order to realize the highest print quality with start of production, the machine builder Giave has developed an innovative pressure control between the cylinders using the standardized interface to the motion control system. This automatically finds the "contact point" between the cylinders electronically with the help of drive data, positioning all chosen decks simultaneously.
CI UV LED
We also offer a central impression configuration as well