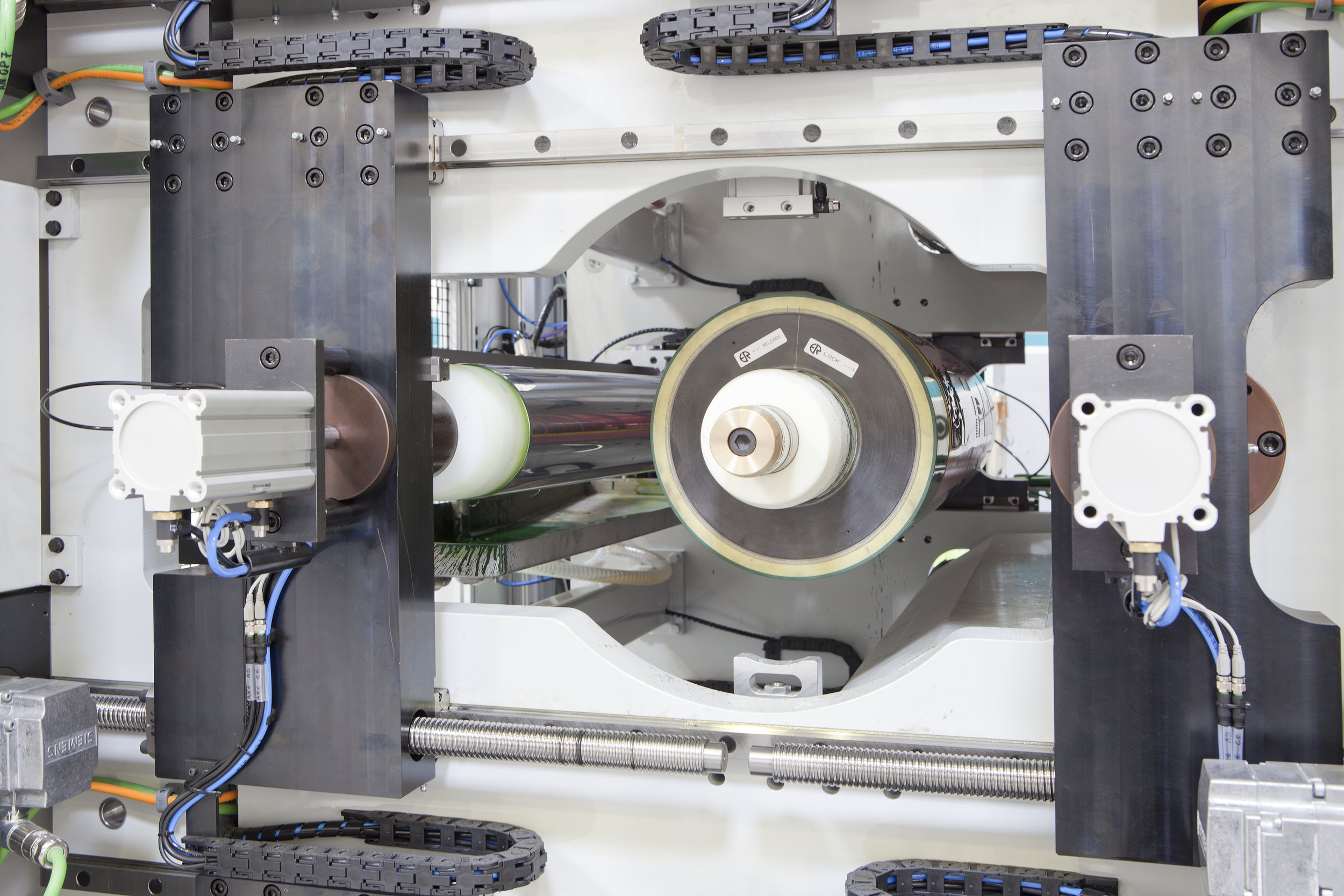
Sleeve Change
Solid deck rails reduce bounce for faster operation
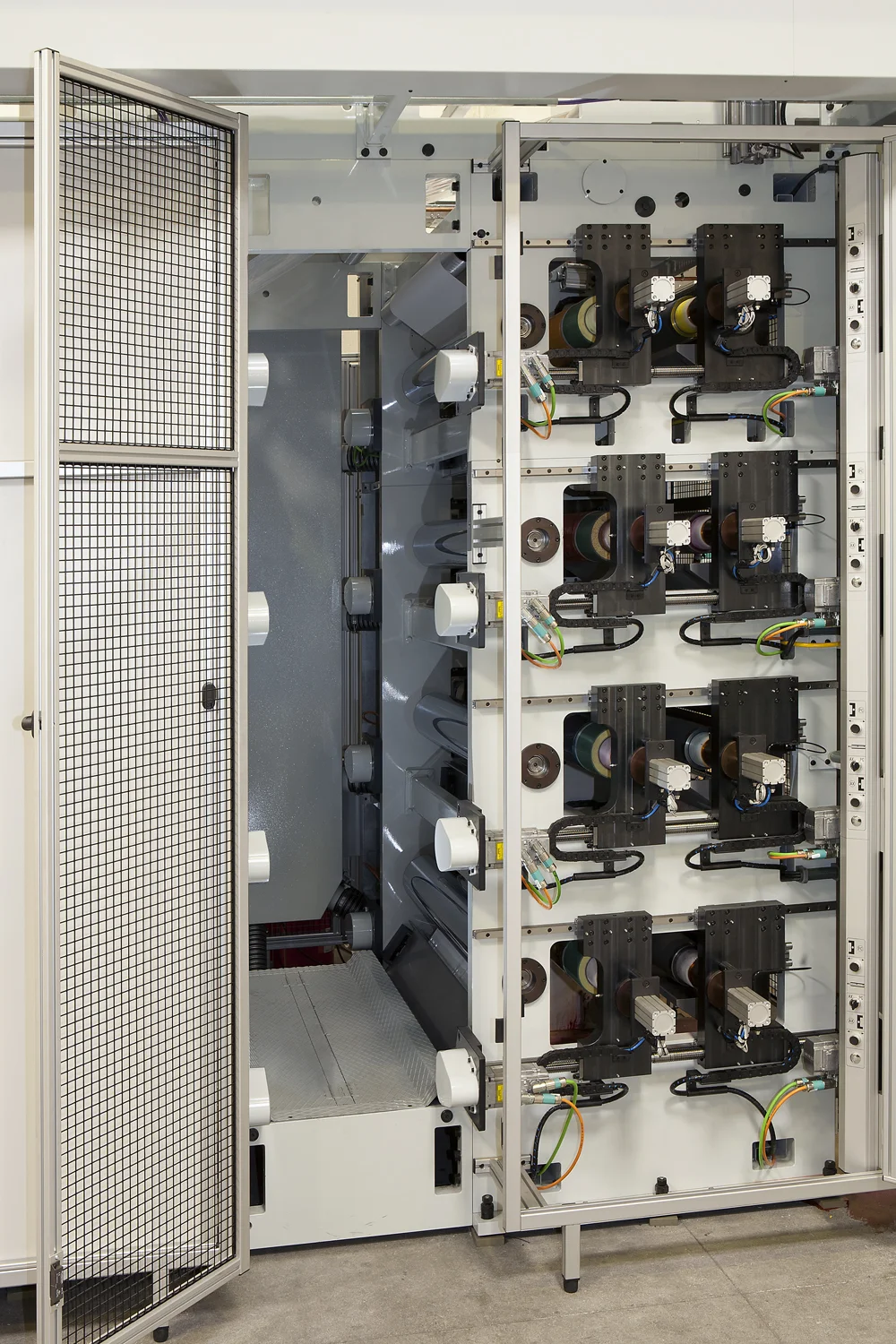
Mono-block design
The heavy mono-block design is engineered to minimize vibrations and bounce while allowing operators access to both sides of the web. This is a unique design compared to legacy stack presses and CI presses for improved troubleshooting.

Easy Cleaning
Easy cleaning and easy web threading
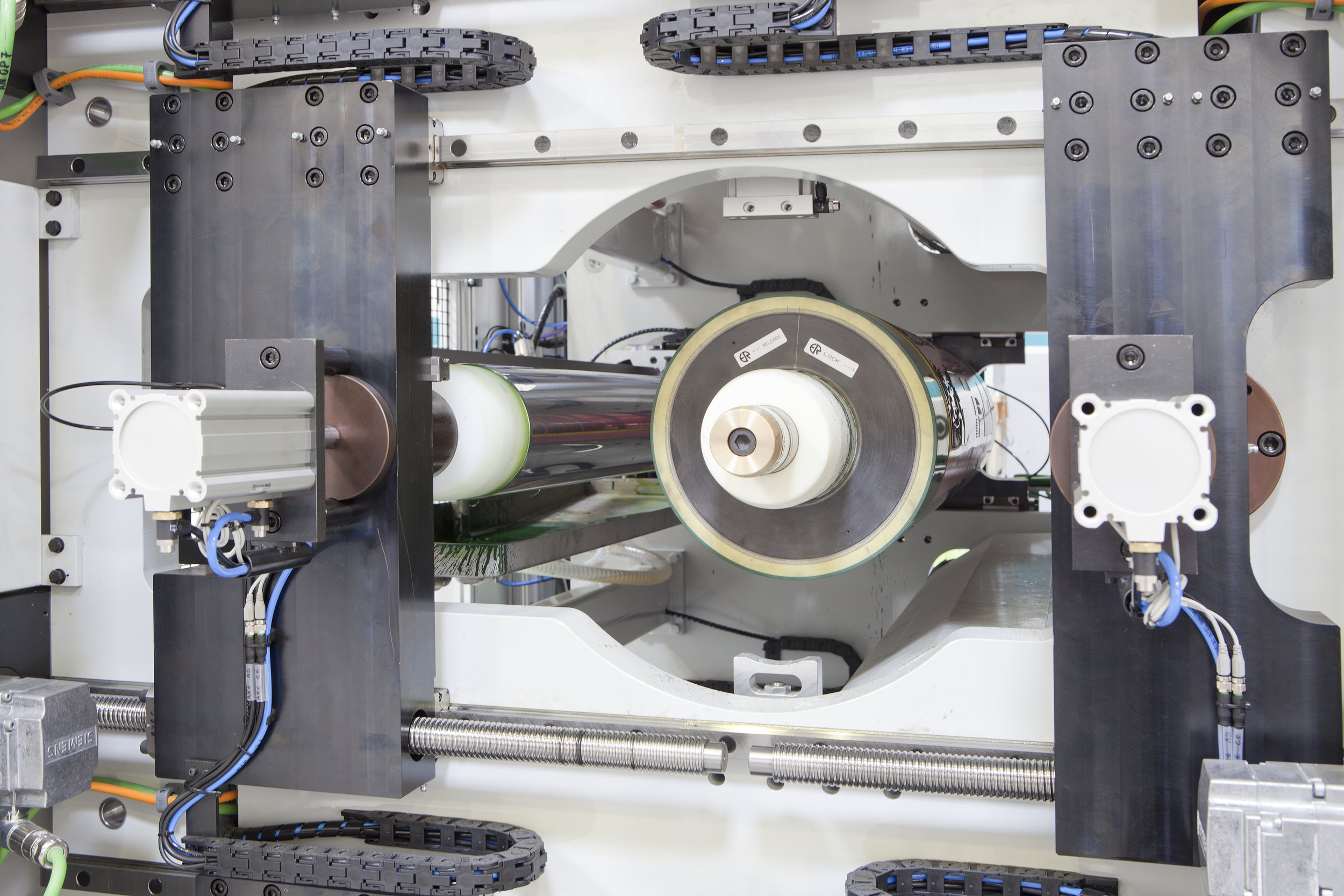
Optional Carbon Fiber Mandrels
Plate nucleus made of carbon fiber

Servo Precision
The all servo decks provide continuous precision and adjustments to the register alignment.

Automatic Cleaning system
Automatic cleaning system integrated in the printing press with an optional advanced system by LR.
Sincroclean® controls the flow of ink at each individual color station according to press speed and ink consumption. It controls the flow of the cleaning solution during the cleaning cycle for cleaning the anilox, enclosed chamber, ink hoses, ink pumps and entire system for the next color change without contamination.
Not only is the pressure controlled, but the cycle time can be chosen by the operator. between 1.5 to 2 gallons of solution per deck for cleaning because of a recirculation and variable speed feature to conserve cleaning solution during the wash up cycles.
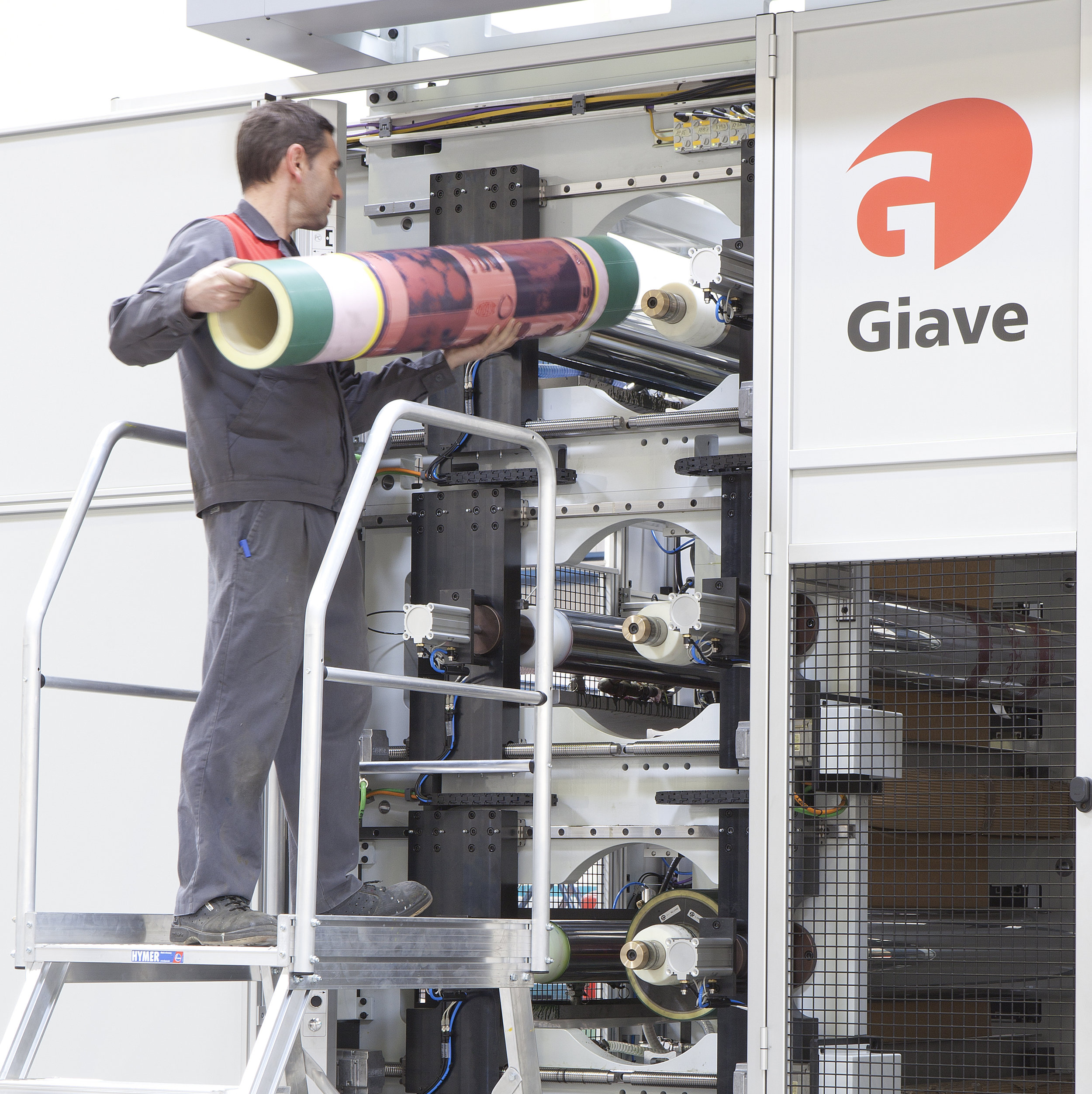
Fast Sleeve Change
Sleeve change is semi-automatic with servo driven motors and wide openings for operator efficiency.

Auto Pre-Register
Automatic pre-register system
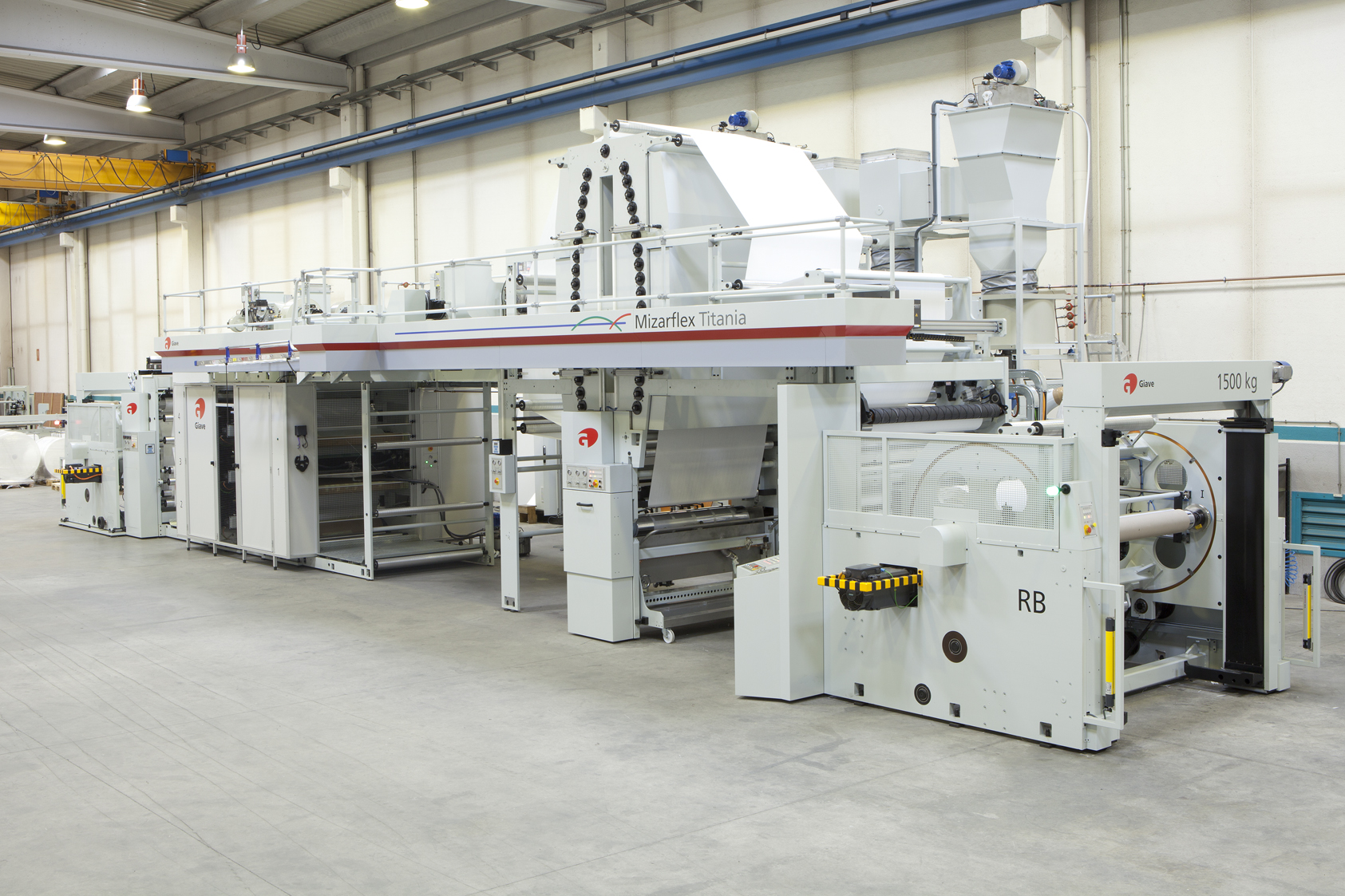
In-line Expansion
In-line special applications (UV, rotogravure, infrared, etc.)
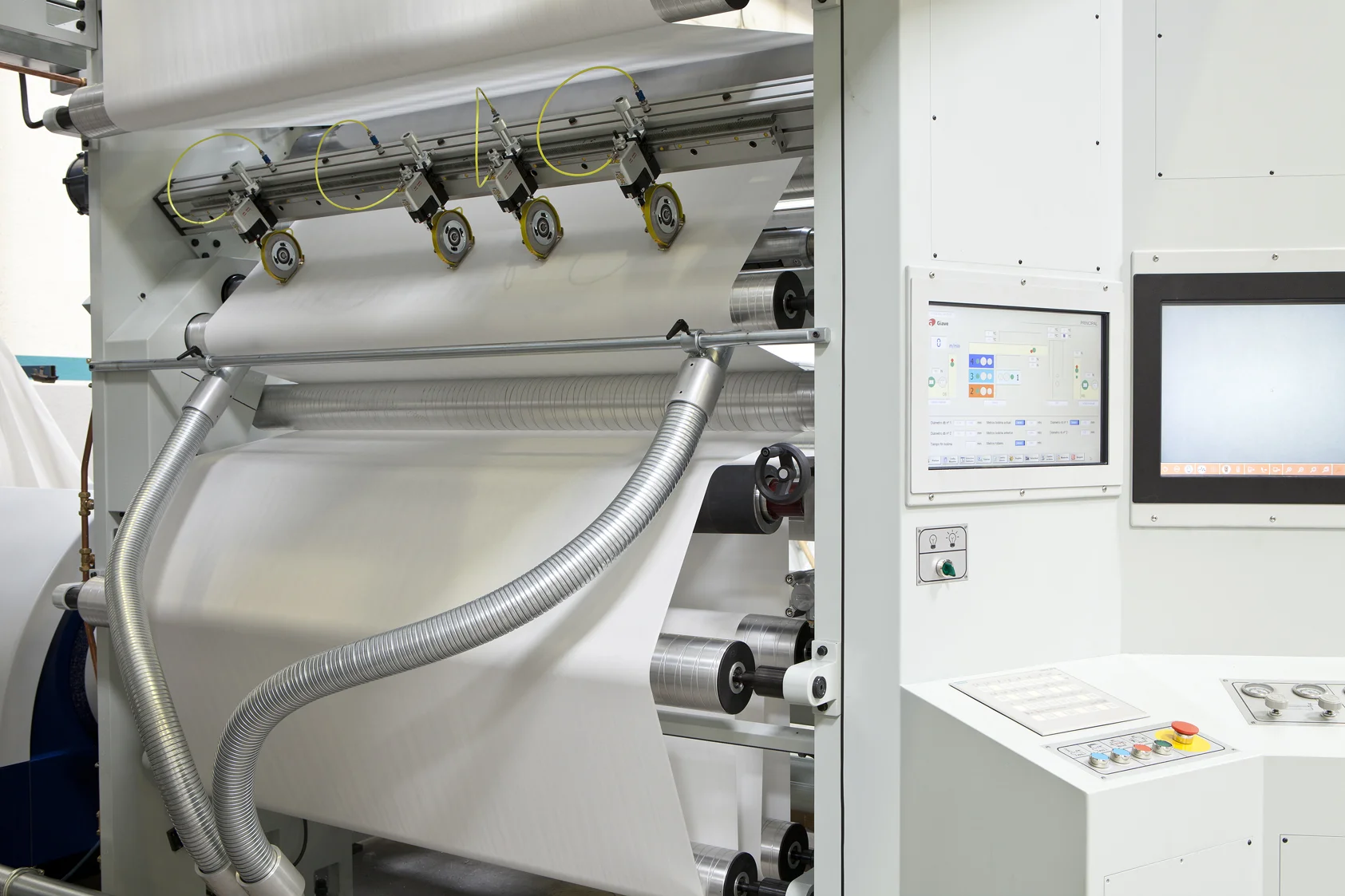
Optional In-Line Web Slice
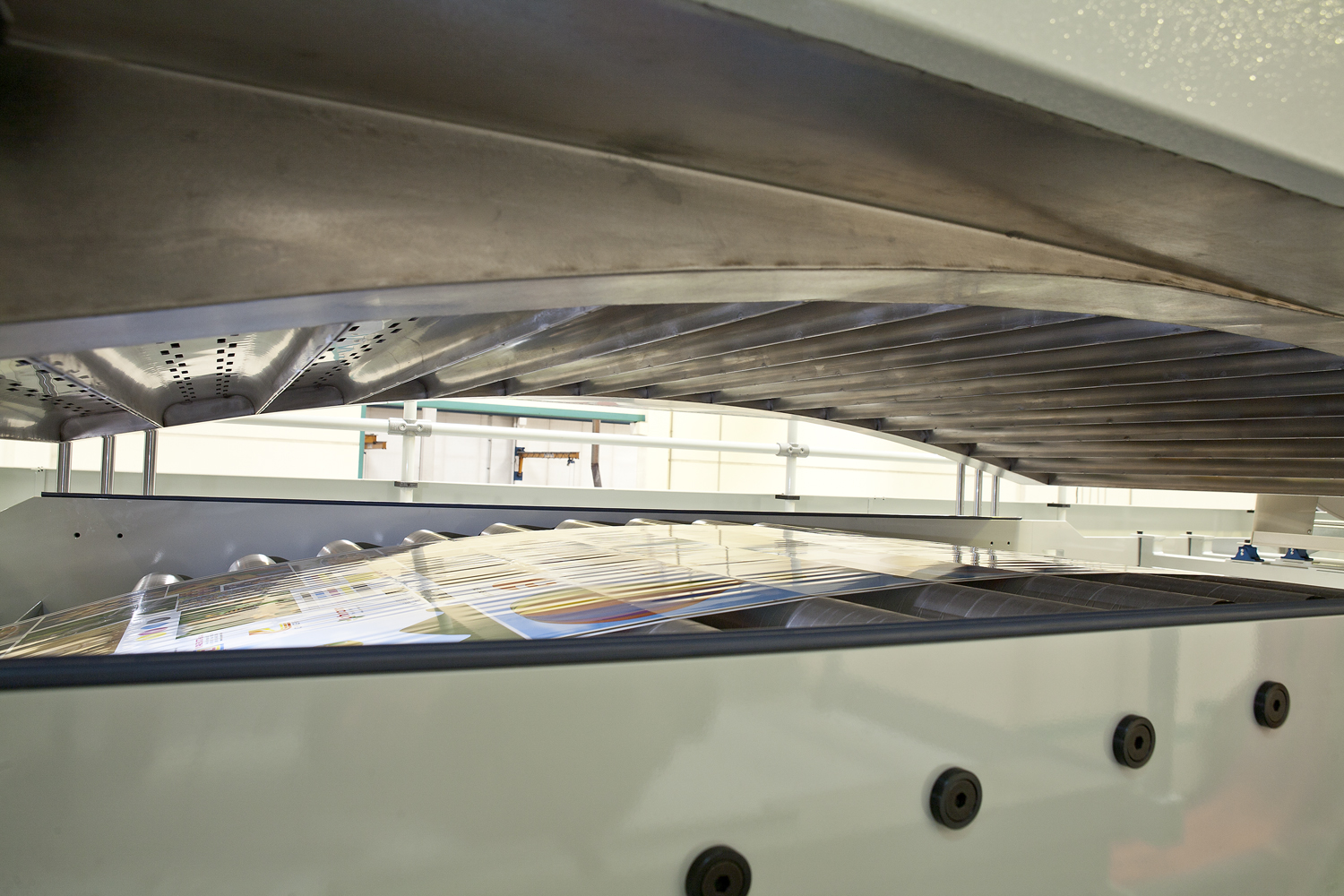
Secondary Dryer
In addition to the in-line dryers, an overhead dryer allows for faster speeds of operation over legacy stack presses.
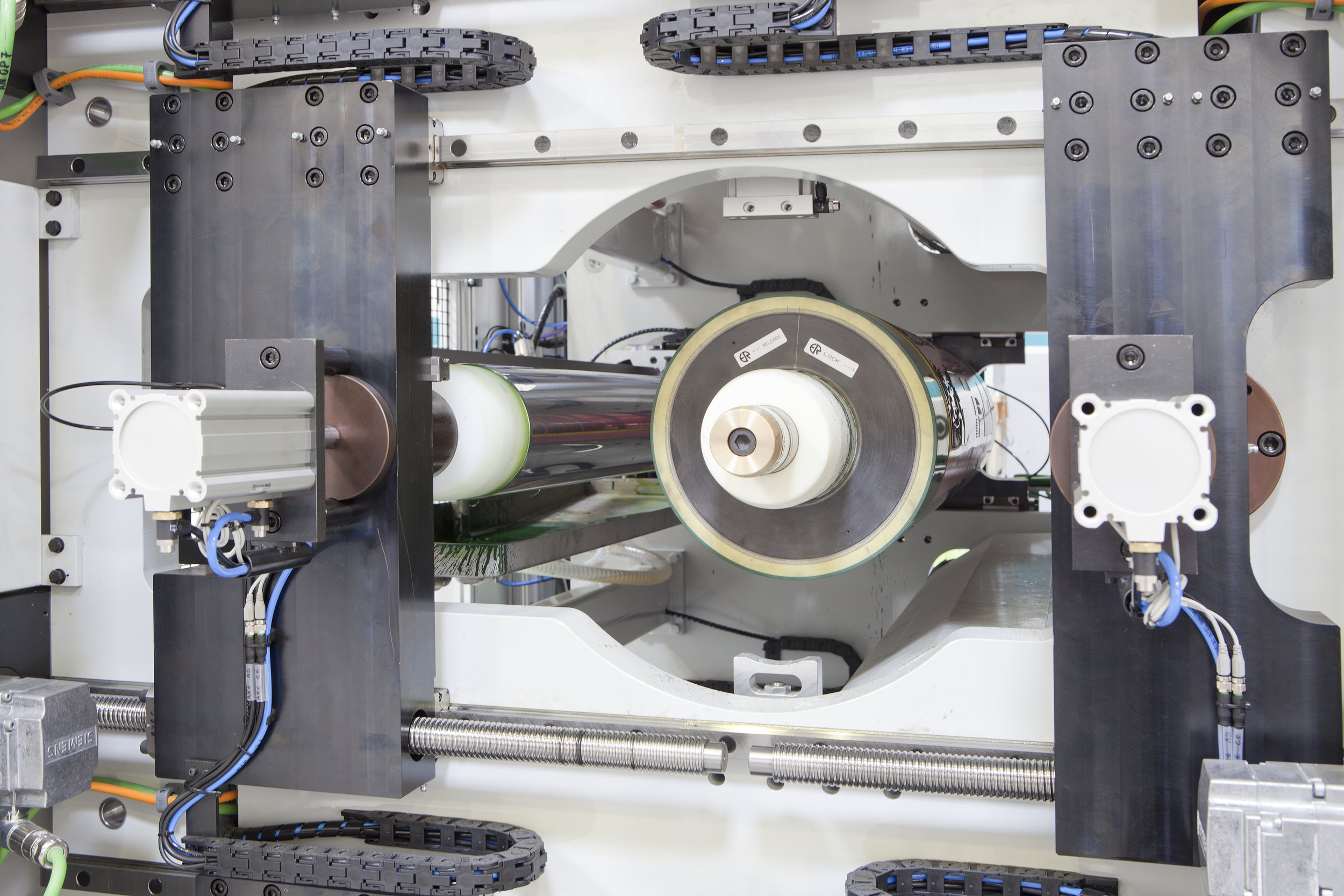
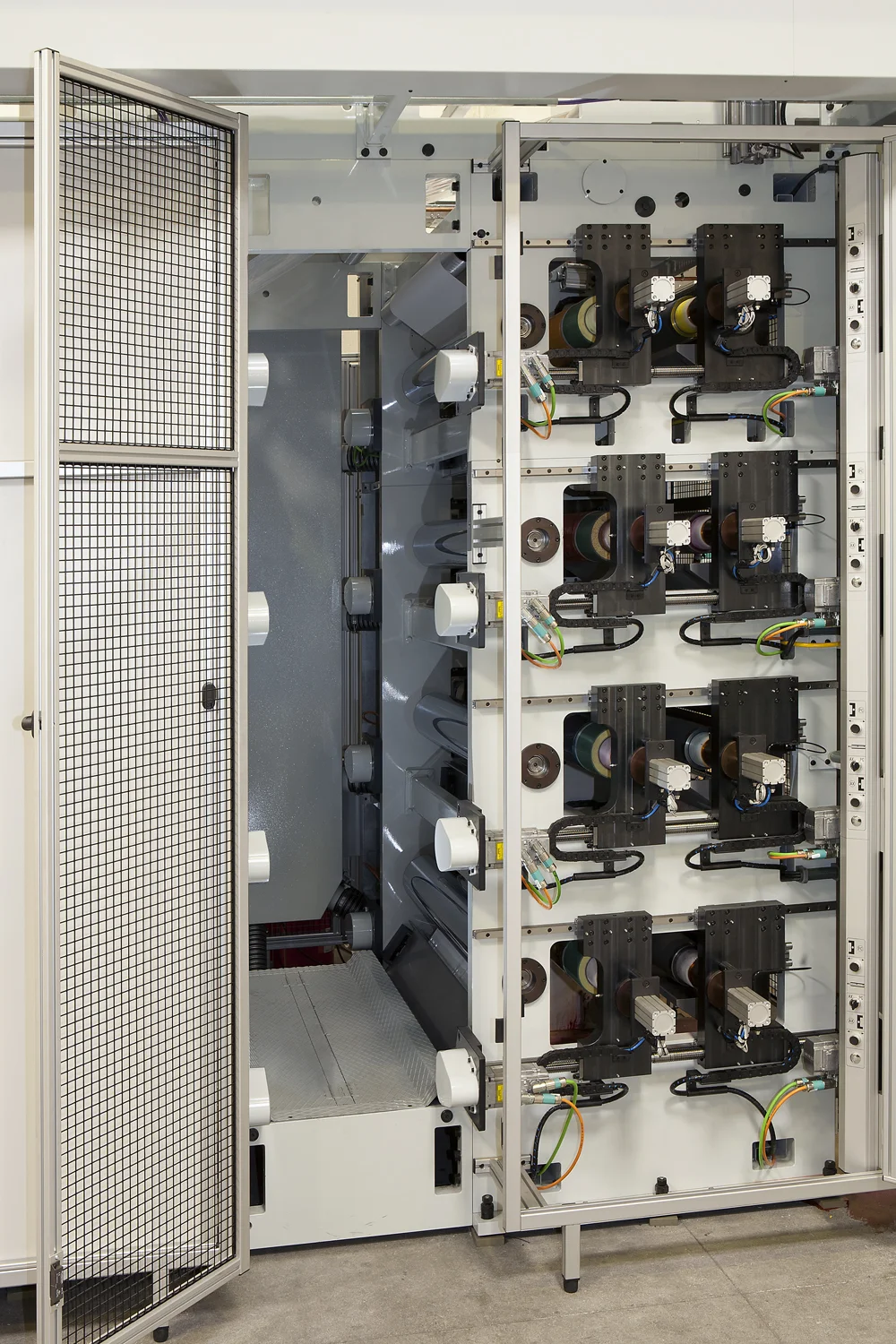

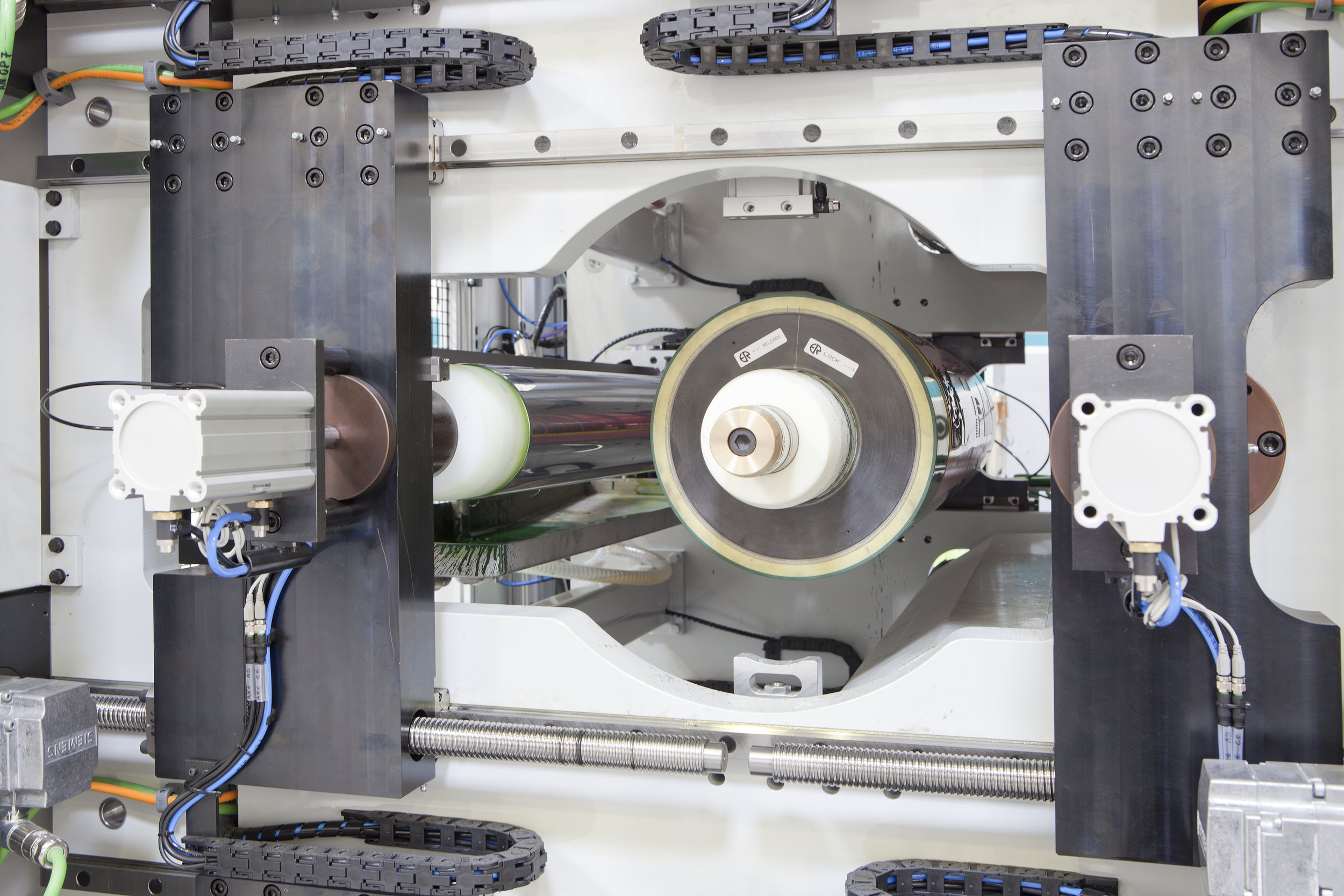


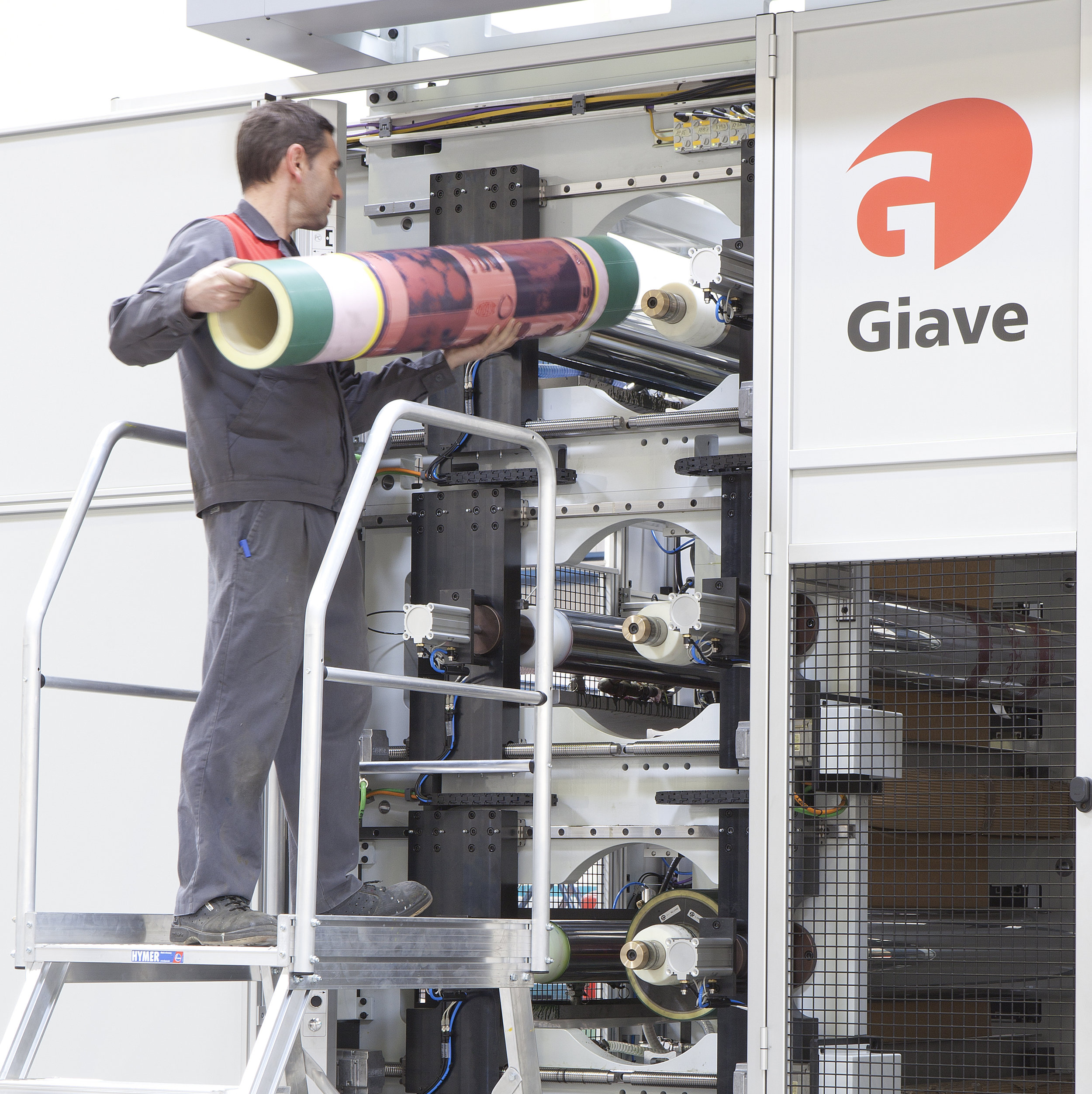

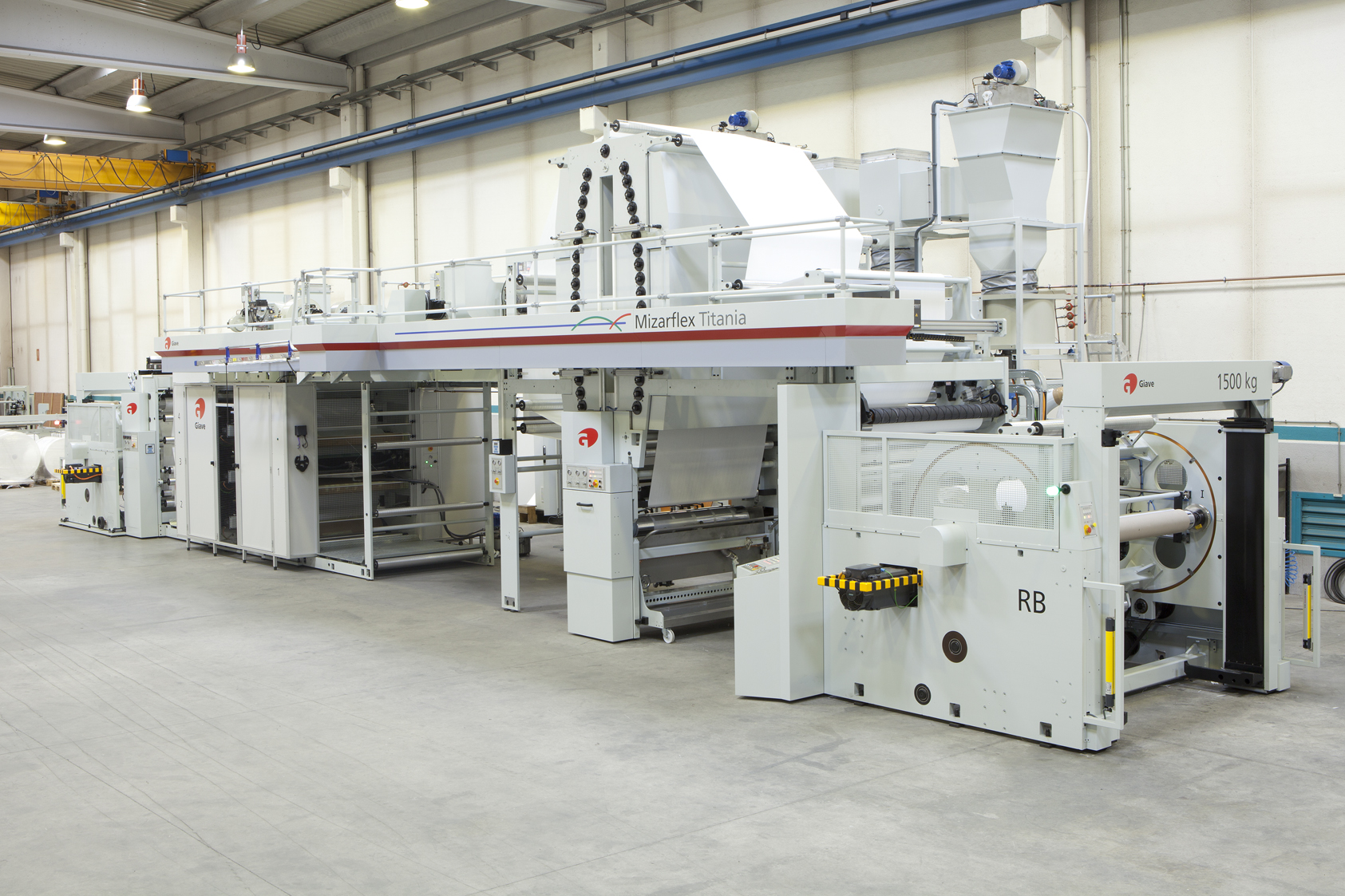
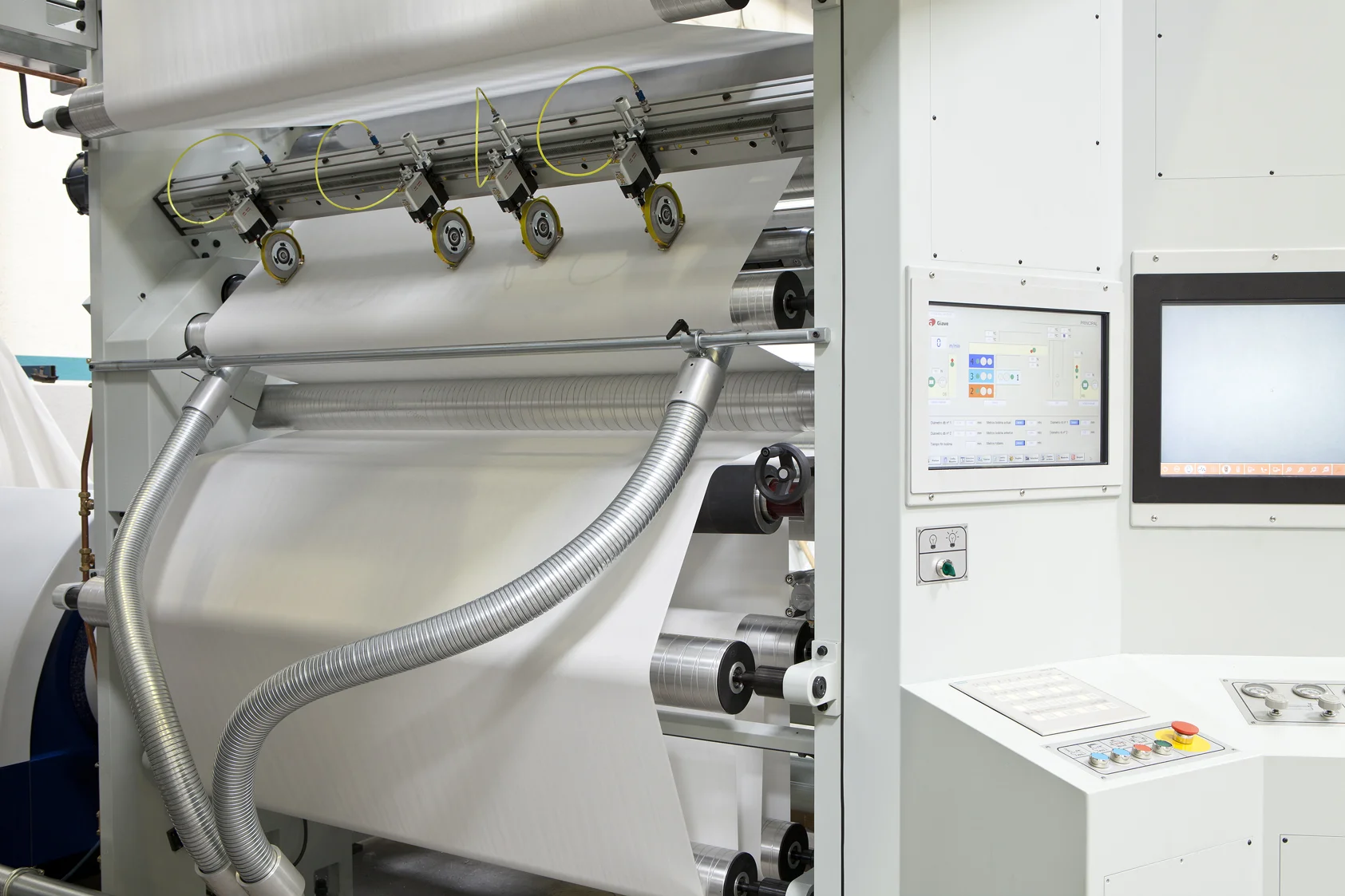
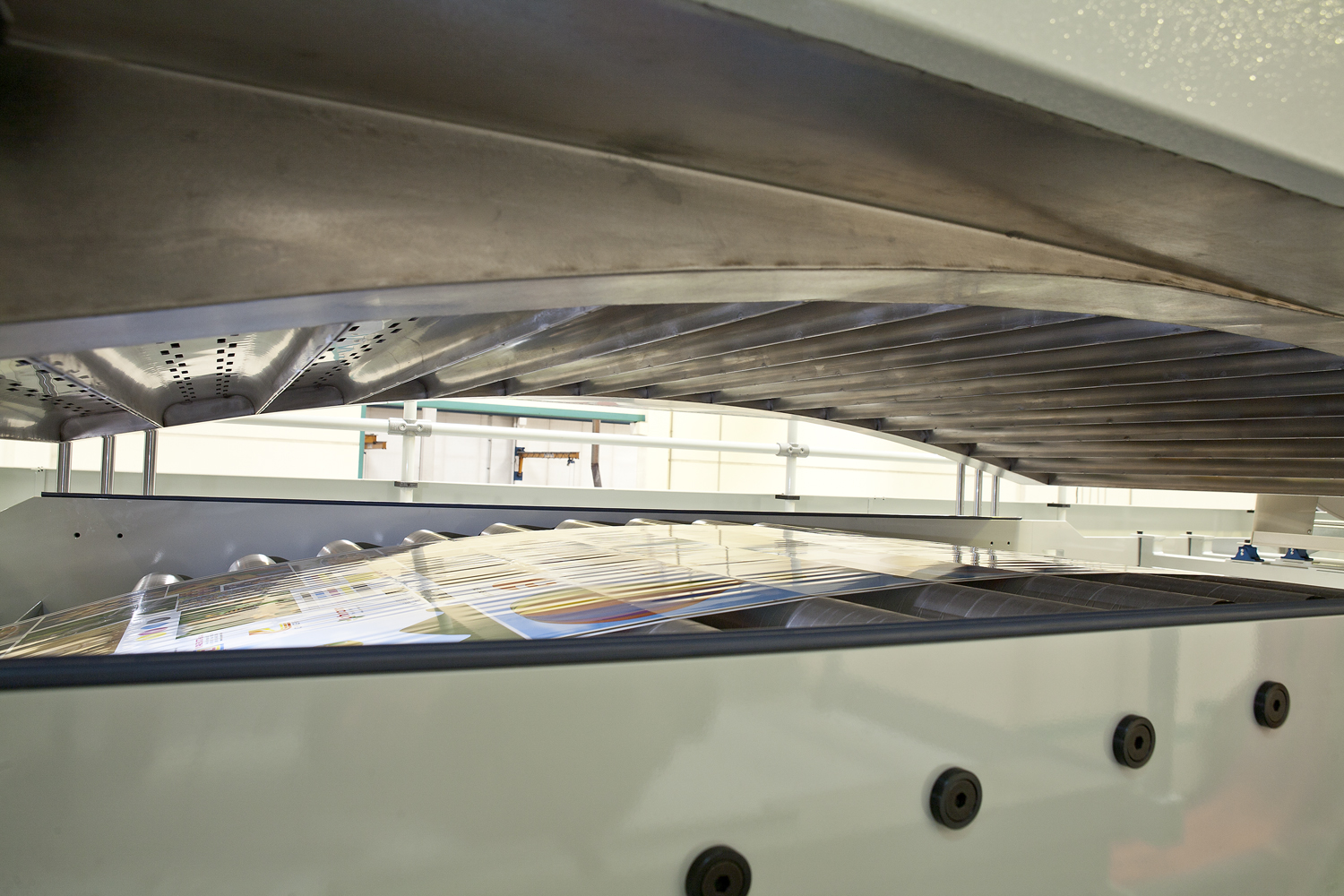